SUCCESS STORIES
Monitoring of surface finishing prevents defective components
Starting point
A company operating worldwide in the field of surface finishing uses Sialogic for the continuous monitoring and optimization of its blasting processes – in particular for the surface hardening of e.g. metal components by irradiation with small abrasive grains. This so-called shot peening process can significantly increase the fatigue strength of the irradiated surfaces and, if applied uniformly, completely prevent cracking, for example. Continuously high process quality, e.g. uniformity of the abrasive used or uniform impact energy of the abrasive on the material to be blasted, are of decisive importance here for the success of the process and for the quality of the products.
Solution
With Sialogic, various consumption and performance parameters of the blast machine as well as performance indicators are permanently recorded, evaluated, monitored and documented for this purpose. By monitoring and evaluating this operating data, a number of process improvements are made possible, including for maintenance, quality assurance, and documentation of process and product quality towards customers.
Achievements
In the area of quality assurance, the use of Sialogic soon paid off: Based on performance parameters that were too low, the malfunction of a single blast turbine of the blast machine could be detected at an early stage and then specifically corrected. As a result, the company was able to avoid the production of faulty parts and prevent enormous consequential damage – caused, for example, by costly recalls and repairs. Operating costs, e.g. in the form of energy and abrasive consumption, can now also be better allocated to individual machines and production steps and can thus be optimized accordingly.
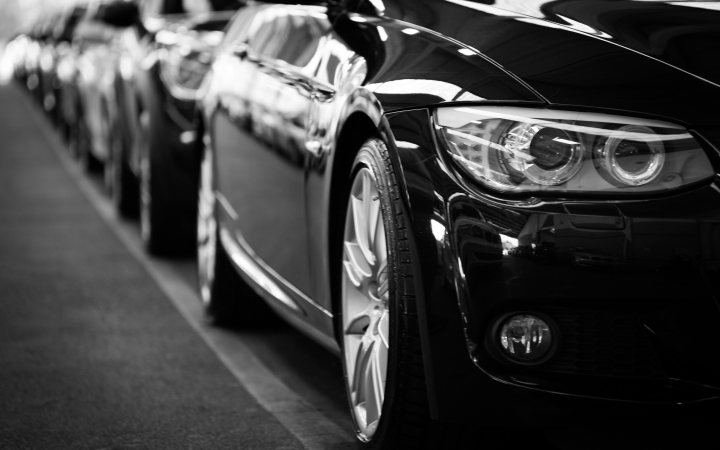
Image: Torsten Dettlaff, Pexels